Which roll of wire fence would you buy?
Do they have the same footage?
If they are the same, why do they look so different?
Not all rolls are created equal. The final diameter of a roll of welded or woven wire fence is determined by four things:
- mesh opening size
- the gauge of the wire used
- the size of the spindle upon which it is wound
- how tightly it is rolled at the end of the assembly line
In the example above, all three rolls of heavy woven wire fence are identical in mesh size, gauge, height, length and weight. They even have the same core openings. And yet they appear to be completely different. The roll on the left is wound very tightly. It is almost half the diameter of the right hand roll which is wound under less tension. If you were to buy one of these rolls, which would you choose? Would you prefer the smaller roll because it is more compact and easier to handle? Or would you choose the larger roll because it looks as if it has extra footage?
Different wire mills may have different size spindles. And they may roll their product under different tensions. So if you see wire fence products in the store that are labeled with the same gauge, mesh size, width and length, they may look very different. A quick way to tell is to check the weight of each roll.
Imported wire fence is usually very tightly wound. Rolls have a small diameter hollow core. This saves space, allowing more rolls to fit on a pallet. Higher density per cubic foot enables more pieces to be loaded in a container, cutting shipping cost per piece.
Have you ever encountered this when buying wire fence?
Which one did you buy and why?
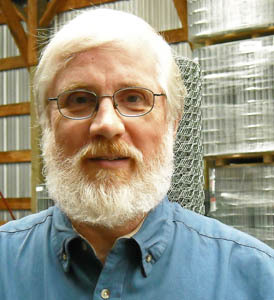
